Plasma surface activation
Lack of wettability or adhesion
Many industrial materials have relatively chemically inert surfaces. As a result, they are not naturally very good at bonding with glue, adhesive, paint or varnish. In general, they are characterised as having a low surface energy.
This characteristic applies to many polymeric materials (plastics), as shown in the following table, which expresses surface energy in mN/m (or dynes) or in the contact angle of a drop of water. The lower the surface energy, the greater the contact angle.
Discover our plasma surface treatment !
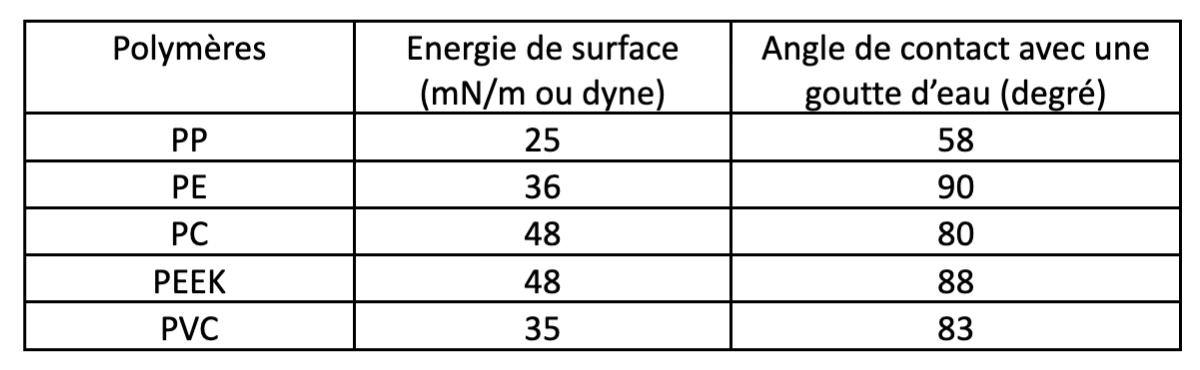
In reality, there are very few materials that are not affected by a lack of adhesion during their industrial transformation cycle. This non- exhaustive list includes :
- elastomers (EPDM, NBR, TPU, etc.)
- ferrous metals, aluminium or other non-ferrous metals
- glass
- composites of any kind
Improving adhesion is therefore a problem faced by many industries. Glass is used in the automotive, packaging and high-tech industries (screens, etc.). Composites are essential in aeronautics, space, sporting goods and mobility.
One solution to the problem of lack of adhesion is plasma surface activation.
What does plasma surface activation involve?
Plasma surface activation is a process that consists of temporarily or permanently modifying the chemical nature of the extreme surface of a material to make it capable of adhering to organic or inorganic substances. The surface modifications take the form of chemical radicals grafted onto the surface. Sufficient to promote adhesion, the grafting rate is low enough for the chemical nature of the surface to remain virtually unchanged. The macroscopic properties of the material (mechanical, electrical, optical, tribological, etc.) also remain unchanged.
Due to the nanometric nature of these modifications, the identification of plasma-grafted chemical radicals requires advanced surface analysis methods (XPS, ESCA, ToF-SIMS, etc.) to determine their nature. The most common are :
- Carboxylic acid
- Alcohol
- Amide
- Amine
- Ketone
- Esther
- Hydoxyl
- Imides
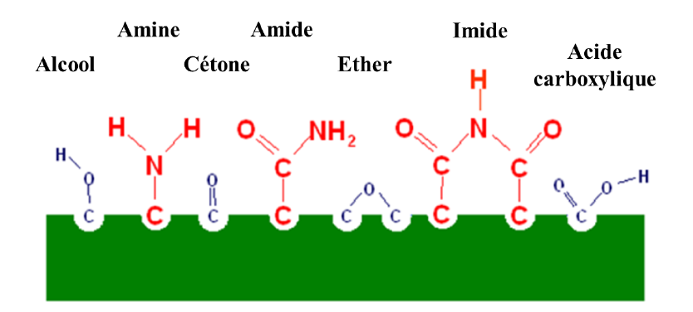
Surface activation by plasma is a chemical process in two consecutive steps using a gas. This is usually compressed air.
In the first stage, the gas is partially ionised by an electrical discharge. Most often, this electrical discharge occurs between 2 electrodes connected to a generator delivering electrical energy at high voltage. This ionisation gives the gas, which is initially chemically inactive, a chemical activity that is only available for a short time. It is used in the second stage of the process, when the gas is blown and brought into contact with the surface to be activated. The chemical activity of the gas causes a chemical change in the surface.
How does plasma surface activation work?
Dry process treatment
In contrast to surface treatment using liquid chemicals, the plasma surface activation process uses only gases and electrical energy: it is referred to as dry surface treatment. This is a major advantage when it comes to reducing the carbon footprint of an industrial process.